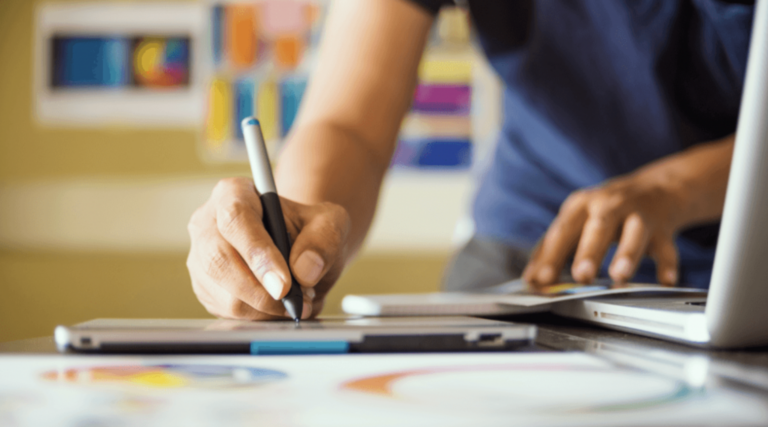
How to design and build a store fixture: Design, Prototype, Test rollout, Final rollout
Designing fixtures for your retail stores takes planning and testing to ensure they meet your needs. Here are the key stages to take a fixture from concept all the way to installation…